The Basic Principles Of Alcast Company
The Basic Principles Of Alcast Company
Blog Article
The Ultimate Guide To Alcast Company
Table of ContentsFascination About Alcast CompanyAlcast Company for DummiesSome Known Questions About Alcast Company.How Alcast Company can Save You Time, Stress, and Money.Fascination About Alcast CompanyThe Main Principles Of Alcast Company
Chemical Comparison of Cast Aluminum Alloys Silicon promotes castability by reducing the alloy's melting temperature level and boosting fluidity during spreading. In addition, silicon contributes to the alloy's stamina and wear resistance, making it beneficial in applications where toughness is crucial, such as automotive components and engine parts.It additionally boosts the machinability of the alloy, making it less complicated to refine into finished products. This way, iron adds to the total workability of light weight aluminum alloys. Copper enhances electrical conductivity, making it helpful in electric applications. It also improves corrosion resistance and contributes to the alloy's total stamina.
Manganese adds to the strength of light weight aluminum alloys and enhances workability. Magnesium is a light-weight component that offers toughness and effect resistance to light weight aluminum alloys.
Fascination About Alcast Company
It permits the manufacturing of lightweight elements with excellent mechanical homes. Zinc boosts the castability of light weight aluminum alloys and helps manage the solidification procedure throughout casting. It enhances the alloy's toughness and hardness. It is typically located in applications where intricate forms and great details are needed, such as ornamental spreadings and specific automotive parts.
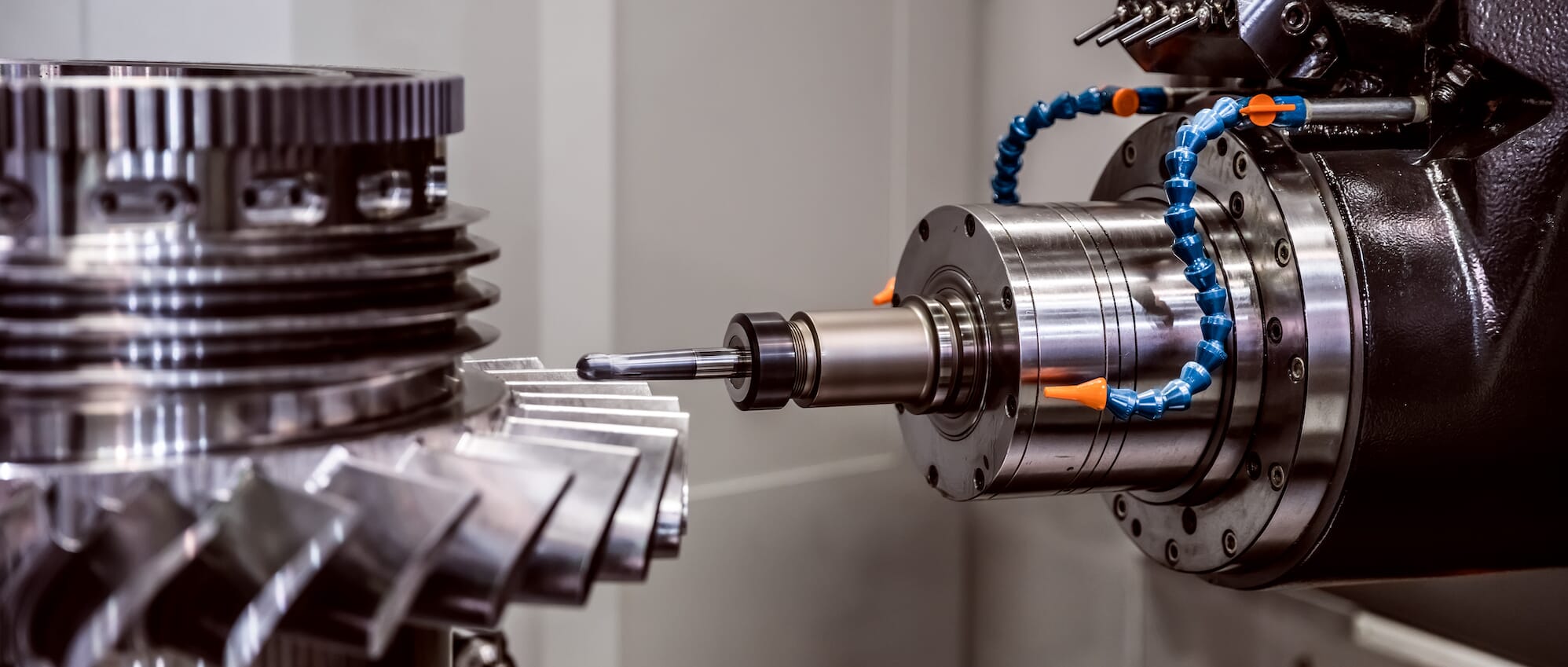
The key thermal conductivity, tensile strength, return stamina, and prolongation vary. Select ideal basic materials according to the efficiency of the target item generated. Amongst the above alloys, A356 has the highest thermal conductivity, and A380 and ADC12 have the lowest. The tensile limitation is the contrary. A360 has the most effective yield stamina and the highest prolongation rate.
The Definitive Guide for Alcast Company
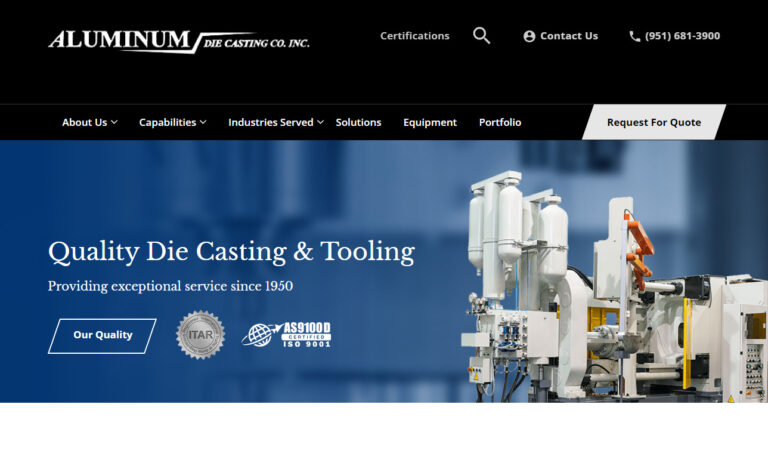
In accuracy casting, 6063 is fit for applications where intricate geometries and high-quality surface area coatings are extremely important. Examples include telecommunication units, where the alloy's exceptional formability enables smooth and aesthetically pleasing layouts while keeping architectural stability. In a similar way, in the Illumination Solutions industry, precision-cast 6063 elements produce elegant and efficient illumination components that call for detailed shapes and good thermal performance.
The A360 exhibits remarkable prolongation, making it optimal for complicated and thin-walled parts. In precision spreading applications, A360 is you could look here fit for markets such as Customer Electronics, Telecommunication, and Power Tools.
What Does Alcast Company Mean?
Its distinct residential properties make A360 an important choice for precision spreading in these sectors, improving item toughness and quality. Aluminum alloy 380, or A380, is a commonly used spreading alloy with numerous unique characteristics. It provides excellent castability, making it a perfect option for accuracy spreading. A380 displays great fluidness when molten, ensuring elaborate and thorough molds are accurately duplicated.
In precision casting, light weight aluminum 413 shines in the Consumer Electronic Devices and Power Devices sectors. It's commonly used to craft intricate elements like smart device housings, camera bodies, and power tool coverings. Its accuracy is amazing, with limited tolerances as much as 0.01 mm, ensuring remarkable product assembly. This alloy's premium corrosion resistance makes it an exceptional choice for outside applications, guaranteeing long-lasting, sturdy products in the discussed industries.
What Does Alcast Company Do?
Once you have decided that the light weight aluminum die casting procedure appropriates for your task, a crucial next step is making a decision on the most ideal alloy. The aluminum alloy you select will considerably impact both the casting process and the residential or commercial properties of the last item. Due to this, you should make your choice carefully and take an educated technique.
Figuring out one of the most ideal light weight aluminum alloy for your application will certainly suggest weighing a broad range of features. These comparative alloy qualities comply with the North American Pass Away Casting Organization's guidelines, and we've split them right into two categories. The first category addresses alloy attributes that affect the manufacturing process. The 2nd covers attributes influencing the properties of the end product.
The Buzz on Alcast Company
The alloy you pick for die casting straight impacts several elements of the spreading process, like just how simple the alloy is to deal with and if it is susceptible to casting flaws. Hot fracturing, also referred to as solidification breaking, is a typical die spreading problem for aluminum alloys that can cause inner or surface-level rips or splits.
Particular aluminum alloys are more susceptible to warm cracking than others, and your choice should consider this. An additional common flaw located in the die spreading of light weight aluminum is die soldering, which is when the cast adheres to the die wall surfaces and makes ejection challenging. It can damage both the actors and the die, so you need to look for alloys with high anti-soldering homes.
Deterioration resistance, which is already a remarkable attribute of light weight aluminum, can vary considerably from alloy to alloy and is an essential characteristic to take into consideration depending on the ecological conditions your item will be exposed to (aluminum casting company). Use resistance is another home commonly sought in aluminum products and can separate some alloys
Report this page